1.What are the lagging indicators in safety performance measurement?
Lagging indicators measure the occurrence of events or activities in the past and their frequency .The lagging indicator can be the number of illnesses in a workplace, or number of Accidents that have happened in a given organization, or even the number of fatalities that have happened within a certain period in an organization and so on.
2.How do lagging indicators differ from leading indicators?
Lagging indicators differ from leading indicators because the lagging indicators measure the statistics of an event that has happened; where as the leading indicators prevent an event or an activity from happening. Leading indicators are used to drive a change in an organization, but lagging indicator is used to measure effectiveness.
ALSO READ:
- Safety culture development in a workplace
- What is Occupational health and safety?
- How to calculate man hours in (hse) safety
3.What are some common examples of lagging indicators in the workplace?
Examples of lagging indicators include accident rate, incident rate, sickness record, workers’ compensation claims filed, regulatory fines incurred, lost work days due to injuries or illnesses, near-miss reports, lost time injury rate, etc.
4.Why are lagging indicators important for evaluating safety performance?
Lagging indicators are important in evaluating safety performance because they provide detailed insight into the effectiveness of an organization’s safety program and as well as offering the necessary improvements to keep the working environment safe at all times.
5.How can the incident rate be used as a lagging indicator?
An incident rate shows you the number of incidents and the frequency of that incident that happened in a workplace over time. You can only know the incidents and their frequency until they have occurred. So, the incident rate is used as a lagging indicator to monitor safety performance.
6.What is the significance of tracking lost time injury frequency rate?
Lost time injury frequency rate is the number of Lost time injuries that occur during the reporting time over total hours worked by the employees. Tracking the lost time injury frequency rate has significance in the sense that the higher the lost time injury frequency rates, the easier for an organization to have an injury among their workers. So, every organization should do everything possible to reduce their lost time injury frequency rate. Engaging in activities like building a robust safety culture, conducting regular hazard assessments, and investing in workers’ safety training can help to reduce the lost time injury frequency rate.
7.How do you calculate the total recordable incident rate?
Total recordable incident rates, according to OSHA, are the total number of Recordable incidents multiplied by 200,000 over the total number of hours worked in a given year. So, if your total number of recordable incidents for the year is 5 and the total number of hours worked for your company is 500000, then your formula would look like this:
5 X 200000 / 500000 = 2
The TRIR is 2.
8.What role does severity rate play as a lagging indicator?
Severity rate is a metric used to quantify the gravity of workplace injuries. In simple terms, severity rate is expressed as the number of Lost work days per certain number of hours worked. Severity rate is a lagging indicator because it gives information about an event that has happened already. The severity rate helps to identify the high-risk areas in organizational activities and encourages control measures to be put in place. It can be used in benchmarking safety performance against industry standards.
9.How can the number of workers’ compensation claims be used as a lagging indicator?
Workers’ compensation claims give us an idea of the workers who are injured or who become ill as a result of their job and the various benefits that were given to them as a result of an accident. It can cover medical costs, Healthcare benefits, disability pay, income, and educational retraining. So, worker’s companies serve as a lagging indicator.
10.What are the limitations of relying solely on lagging indicators for safety performance?
The truth is that in monitoring safety performance, so many metrics are being deployed in order to achieve that, and these metrics can fall into lagging or leading indicators. There is need to deploy both lagging and leading indicators to monitor safety performance.So, in a nutshell engaging lagging indicators and leading indicators and any other thing we improve the safety performance monitoring.
11.How can lagging indicators help identify trends in workplace safety?
There are so many ways a lagging indicator can be used to monitor or to identify trends in workplace safety. For instance, having recordable injuries and illnesses in an organization is a lagging indicator; monitoring this data over time can help the organization to know whether if their safety programs and initiatives are helping them to reduce injuries and illnesses or otherwise. If a company has ten recordable injuries and illnesses in the year 2018, with good safety initiatives in place, if this number is reduced by half by the next year, that means there is an improvement within that company.
12.How often should lagging indicators be reviewed and analyzed?
All lagging indicators should be reviewed and analyzed as soon as possible So that it will help to keep the company in check and to let them know whether their safety programs and activities are really improving the system.
13.How can companies ensure the accuracy of their lagging indicator data?
The companies can ensure the accuracy of their lagging indicator data by ensuring that proper documentation has been provided for these records. Train workers on incident reporting on site. Ensure that every worker knows what to do whenever there is an incident. Proper communication should be in place. Update the incident or statistics record frequently.
14.How do lagging indicators influence safety policies and procedures?
Lagging indicators being a reactive approach, can help influence safety policies and procedures in a workplace. Policies can be reviewed when there is an increase in one of the lagging indicators. Procedures can also be written or reviewed following the result of a certain lagging indicator.
ALSO READ
- Safety culture development in a workplace
- What is Occupational health and safety?
- How to become a health and safety consultant (HSC) in the UK
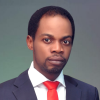
Onyeka Emma is a QHSE Professional with more than 10 years of experience in occupational health and safety, which spans many industries such as construction, beverage, oil and gas, etc. He has many health and safety certifications, including NEBOSH IGC, ISO 9001:2015, ISO 14001:2015, and ISO 45001:2018 Lead auditor certificate. A member of IOSH, ISPON, and Nigeria Red Cross Society. He is interested in business, entrepreneurship, Speaking, and motivating people to do better for themselves. He enjoys leisure with a good motivational book.