How to identify hazards on a work site
Hazard identification on site is paramount for you if you are to put control over them. You can only control a hazard that you have identified around you.
Well, hazards are actions, situations, things, objects or activities that can cause harm to people or damage material and machines in the workplace.
In this article, you’ll learn how to identify these hazards using the following techniques below.
- Observation.
- Task analysis.
- Checklist.
- Incident and near-misses.
- Failure tracing techniques.
There are different categories of hazards in the workplace. They include
- Safety hazards.
- Biological hazards.
- Physical hazards.
- Ergonomic hazards.
- Chemical hazards
Safety hazards.
These hazards include electrical hazards, operating machinery, and trip and fall.
Biological Hazards.
These hazards are substances and diseases associated with working among people, animals or infectious plants.
Physical hazards.
These hazards include loud noise, radiation, and ultraviolet light.
Ergonomic hazards.
These hazards affect employees whose work puts a strain on their bodies. Such work includes heavy lifting or sitting for a prolonged period.
Chemical hazards.
These hazards mainly threaten workers whose roles expose them to dangerous solvents, liquids, or flammable gases.
Here are the five techniques to identify hazards at a work site.
Observation.
Observation is one of the reliable ways to identify hazards. Mostly, it depends on the experience and knowledge of the assessor. A knowledgeable assessor can easily spot hazards. Even much better than one that isn’t knowledgeable and inexperienced.
During observation, the assessor will look at the work on the site, works by individuals and as a group. Doing this will help the assessor get the actual hazards in those activities.
Observation will help the assessor spot other less obvious hazards. Such as fumes, noise and gases in the activities.
Observation will also help check the rules and precautions the worker is disobeying, and not following while working.
Task analysis.
Task analysis can be called job hazard analysis. It analyses a given task in several steps, and the results are used to correct hazards or problems that will give rise to harm while doing the job.
Task hazard analysis is beneficial. It improves the efficiency of the work.
Task analysis results provide a guide in producing a safe work method. It can also help in the redesigning of work areas and on in emergency procedures.
More so, you can use the results from task hazard analysis to provide relevant safety rules on-site. And it serves as a tool for reporting hazards.
Checklist.
Checklists are forms or templates used to carry out an inspection. It covers the inspection issues comprehensively and consistently.
An inspection checklist identifies hazards when you use them correctly. Ensure that your inspection checklist is in a structured manner. In this manner, the inspection process will have an orderly approach.
However, checklists do have some limitations when using them to identify hazards. Sometimes, it can be hard to Identify a Hazard not listed in the inspection checklist. Such are less likely to be seen during the process.
When planning to develop an inspection checklist for an activity, We recommend you look at the four P’s to get a well-structured inspection checklist. These four areas will guide you to produce a comprehensive site inspection checklist.
- Premises– The premises includes access and escape, housekeeping and the working environment.
- Plants and substances– Under this, you’re looking at the use, storage and separation of substances and chemicals.
- Procedures– Procedures are Work Permits, safe work procedures, and personal protective equipment use.
- People– You’re looking at people’s behaviour, health surveillance and authorised personnel for various tasks or jobs.
Incident and near misses reports.
Reports on incidents and near misses are a great tool to identify hazards on site. Though, the incidents and near misses are reactive tools. However, trends from these reports can help during risk assessment activities. And also aid in putting adequate control measures against future similar accidents or incidents.
Government agencies may require you to report certain types of incidents. These are then analysed by them serving useful statistics over different industries.
Failure training techniques.
The failure training technique is one of the complex systems you can use to identify hazards. One of them is called a hazard and operability study (HAZOP)
HAZOP breaks down a system. For example, a chemical process system. It breaks down a chemical process into different sections. And then systematically ask what can go wrong in that section?.
What would be the consequences if things go wrong. And what measures could be introduced to reduce the likelihood of failure happening? And if the system does fail, what might mitigate the consequences.
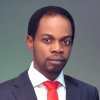
Onyeka Emma is a QHSE Professional with more than 10 years of experience in occupational health and safety, which spans many industries such as construction, beverage, oil and gas, etc. He has many health and safety certifications, including NEBOSH IGC, ISO 9001:2015, ISO 14001:2015, and ISO 45001:2018 Lead auditor certificate. A member of IOSH, ISPON, and Nigeria Red Cross Society. He is interested in business, entrepreneurship, Speaking, and motivating people to do better for themselves. He enjoys leisure with a good motivational book.