What are the leading indicators in the context of workplace safety?
Leading indicators in the context of workplace safety are the various inputs that people are contributing to the ohs of an organization to better the occupational health and management system. Those inputs are Geared towards ensuring that there is an improvement in occupational health and safety. Leading indicators are called proactive measures, unlike lagging indicators, which are reactive measures.
How do leading indicators differ from lagging indicators?
Leading indicators differ from lagging indicators in the following: leading indicators look ahead and try to predict future outcomes but lagging indicators are from what has happened. Leading indicators are proactive measurements, but lagging indicators are reactive measurements. Lagging indicators are handy in determining trends of events, but leading indicators tell you whether your activities are effective at preventing accidents.
Why are leading indicators important for proactive safety management?
Leading indicators are essential for proactive safety management because of the below: They prevent workplace injuries and illnesses from workers. Reduces costs associated with incidents when they happen. It improves the productivity and overall performance of occupational health and safety. It enhances the worker’s participation.
What are typical examples of leading indicators in safety performance?
Some common examples of leading indicators are safety inspection, safety audits, supervision, monitoring, near-miss reports, hazard identification, incident rates, safety monitoring, employee safety observation, training, improvement, safety culture assessment, preventive maintenance programs, job hazard analysis, risk assessment, and method statements.
What is the role of safety audits and inspections as leading indicators?
The role of safety inspection and audit as leading indicators are as follows. Safety inspection assist in determining the cause of Hazard in the workplace. It helps to create employer awareness of the safety in the workplace. Compliance of the system is being tested from inspection. Organizations demonstrate their commitment through safety inspections or audits.
How can monitoring the use of PPE be a leading indicator?
Monitoring of PPE is a proactive activity. When PPE usage is being monitored, first-hand knowledge will be gotten on why workers are not using their PPE or why there should be an improvement of the PPE in use, such as poor quality. Monitoring of PPE usage will encourage the workers to make use of their PPE.
What challenges might an organization face when implementing a leading indicator?
There are various challenges an organization may face when implementing leading indicator data. With leading indicators, there are often few already data for use. The leading indicators are often complicated to measure, and if you are new to your company with no experience, leading indicators may be challenging to work around with. Leading indicators may sometimes be overlooked because the management may need to know whether a particular metric has anything to do with the success of the business.Â
How can leading indicators be used to predict and prevent workplace accidents?
There are various leading indicators, and among them is the job safety analysis. For instance, job safety analysis can be used to predict and prevent workplace accidents because, in it, you can be able to identify hazards involved in a workplace and can be able to put control measures to that Hazard to reduce the risk of harm. So many of the leading indicators can also be used to predict and prevent workplace accidents.
How often should lead indicators be reviewed and analyzed?
The leading indicators should be reviewed and analyzed regularly, and when you have reviewed and analyzed them, you need to share what you have learned from your activities with the workers and the management.
How can an organization ensure the accuracy and reliability of the leading indicators data?
An organization can do this by using various data validation and verification techniques such as auditing, checks, and also documenting every process and result.
ALSO READ:
- Frequently asked questions on Industrial safety helmet.
- Safety culture development in a workplace
- What are safety glasses made of?
What role do leading indicators play in the continuous improvement of safety programs?
Leading indicators are proactive measures in health and safety to predict and prevent injury and illness in the working environment. Because of this role, it helps in the building of safety performance of a given safety management system and in the continuous improvement of occupational health and safety.
How can leading indicators help in developing a strong safety culture?
Leading indicators, being a proactive measurement, can help to develop and build a strong safety culture in many ways, such as ensuring there is training, supervision, and education among employees. Ensures that hazards are identified and control measures are put in place at work. Ensures that the management takes a leading role in health and safety at work.
ALSO READ:
- Frequently asked questions on Industrial safety helmet.
- Safety culture development in a workplace
- What are safety glasses made of?
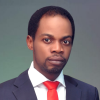
Onyeka Emma is a QHSE Professional with more than 10 years of experience in occupational health and safety, which spans many industries such as construction, beverage, oil and gas, etc. He has many health and safety certifications, including NEBOSH IGC, ISO 9001:2015, ISO 14001:2015, and ISO 45001:2018 Lead auditor certificate. A member of IOSH, ISPON, and Nigeria Red Cross Society. He is interested in business, entrepreneurship, Speaking, and motivating people to do better for themselves. He enjoys leisure with a good motivational book.